在以往的3D打印技术应用中,多数以不影响汽车结构的内饰配件、外形覆盖件等形式呈现,尽管应用的不多,但早已不再是什么前沿技术。不过,保时捷却在3D打印的道路上越走越深入,如今已经应用到了动力系统的核心技术之中。

近些年,很多汽车企业都将3D打印技术应用到了汽车制造上,不过其制造的零件多用于外观套件、内饰零件之中,保时捷也是如此,比如产量较高的718、911的座垫和靠背等。
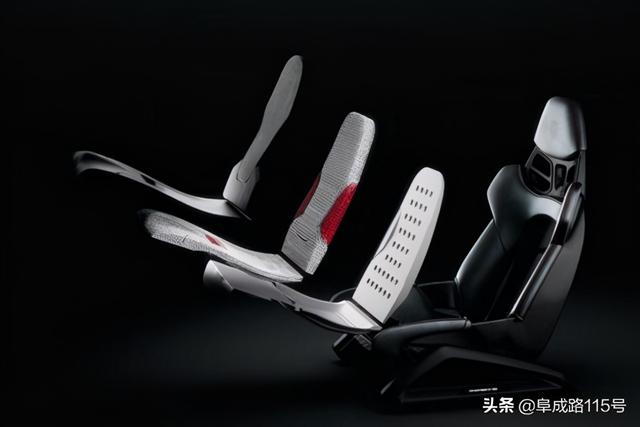
不过就在2018年,保时捷开始联合Mahle(马勒集团)和Trumpf(通快集团),在3D打印技术方面进行合作,并于2019年初,将3D打印出来的部件应用在了911 GT2 RS的发动机之中。


这个部件就是发动机最为重要部件之一的活塞。我们知道,活塞在发动机的运转中起着至关重要的作用,并且,总是处于最为恶劣的高温高压环境之中。我们常见的活塞多以铸铁、高强度钢或铝合金材质打造,并且多数高性能发动机在活塞外侧以及拉杆接触位置应用陶瓷耐磨涂层以增强耐磨性。于是,对于3D打印技术来说,在材质上就与我们常见的树脂或塑料有着本质的不同。


保时捷应用的是高纯度粉末状金属材料。在制造过程中,工程师先在计算机中创建活塞的三维图像,然后通过激光金属融合工艺(LMF)技术,激光束在预制的轮廓中一层一层加热并融化金属粉末,使其最终凝固成完整的活塞轮廓,待冷却后经过打磨而得到活塞成品,整个过程和原理与传统的3D打印技术完全相同。

大阳日酸株式会社成立3D打印实验室
近日,日本大阳日酸株式会社宣布将建立一个全新的3D打印实验室,并将其命名为“增材制造高级室”。据悉该实验室位于日本山梨县,主要研究和开发3D打印技术的中心位置。 大阳日酸设立的增材制造高级室 大阳日酸株式会社是日本最大的工业气体生产商,主要涉及氧
据保时捷官方宣称,以该材料3D打印制造出来的活塞,在保持相同刚性的前提下,在轻量化方面,相比于以前的量产锻造活塞轻10%。此外,由于该活塞是逐层打印的,因此可以实现传统锻造技术难以实现的复杂结构。工程师就在该活塞的顶部设计了封闭式的冷却管道,使之有效降低了活塞局部温度,并优化发动机燃烧效率。使得911 GT2 RS所搭载的3.8L 水平对置6缸双涡轮增压发动机最大功率增加22kW,达到537kW。

时隔一年,随着电气化进程的推进,保时捷还将3D打印技术应用到了纯电驱动系统之中。以Taycan车型为试验蓝本,其中包括电动机、2挡变速器以及控制单元的外壳、轴承、热交换器和冷却系统。

理论上来说,得益于在3D打印过程中,使用激光粉末状的金属熔化并融合成所需形状的制造特性,可以创造出相比于锻造件更复杂的结构部件,比如外壳,在拥有蜂窝状结构,保证散热性和强度的同时,还能够减少重量。

结果是,3D打印制造出的纯电驱动系统相比常规锻造生产出的机型,不仅体积更小、重量更轻,还更坚固,并且通过了保时捷严苛的质量和压力测试。

据保时捷称,3D打印外壳的重量要比锻造式外壳轻40%,从而使整个纯电驱动系统的重量减少了10%。同时,将电动机和变速器部分的刚性提升了一倍。由于能够在驱动单元中集成更多部件,令组装时间减少了20分钟,降低了生产成本。

尽管3D打印技术优势明显,但是以目前的技术和产业布局,仍实现不了大规模生产。目前,此技术只适合用于生产小批量车型所需的零部件。不过,随着产业技术的升级,3D打印技术一定会走向量产化,或许到那时,我们所购买的汽车不仅成本更加低廉,也许还会实现真正的以人为本的定制化。