中科院通过3-D打印的紫外线可固化牺牲模制作量身定制的可穿戴传感器
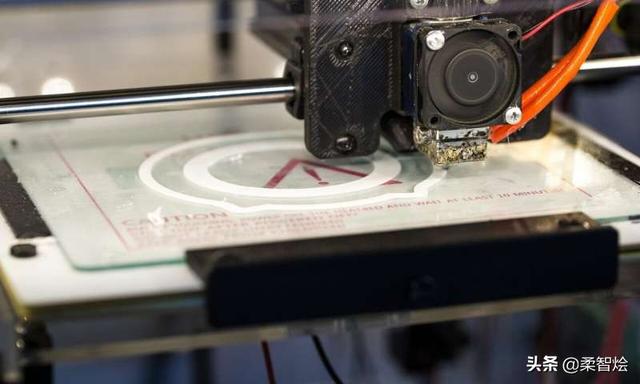
与传统工艺相比,三维(3-D)打印技术具有定制和复杂设计的可穿戴传感器制造能力。桶式光聚合3-D打印技术具有更好的打印分辨率,更快的打印速度,并且能够制造精细的结构。由于缺乏高导电性的光固化树脂,因此很难通过大桶光聚合3 D打印技术制备传感器。
在《Advanced Functional Materials,》上发表的一项研究中,由中国科学院福建物质结构研究所(FJIRSM)的吴立新教授领导的研究小组开发了具有高拉伸性的多孔挠性应变传感器(PFSS)。极好的可恢复性。
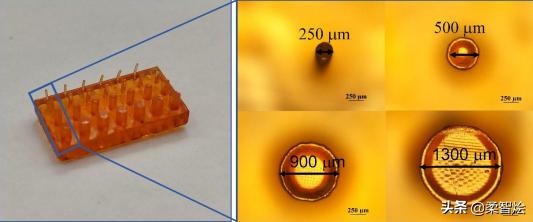
(a) 不同直径的3D打印圆柱(ACMO-HUA)(1.3毫米、0.9毫米、0.5毫米和0.25毫米)。(b) 印刷圆筒的光学图像.
3D打印零件如何帮布加迪实现0.67kg/PS的重量/功率比
借助布加迪Bolide的技术概念,法国豪华车制造商现在提供了以下问题的答案:“布加迪是否会在其标志性的8.0升w16发动机周围制造出轻巧的车辆?布加迪飞利德(Bugatti Bolide)的实验研究是一款面向轨道的超级跑车,其特征是采用w16发动机,该发动机是作为动力
研究人员首先合成了一种可水解受阻的丙烯酸脲双功能单体,以形成交联的聚合物网络,从而防止印刷零件在未固化的树脂中溶解。3-D打印的支架可以在热水中水解,这为牺牲模具提供了有吸引力的选择。然后,他们在模具中浇铸聚氨酯/碳纳米管复合材料,以制备柔性传感器作为PFSS。该PFSS在低压缩应变下显示出良好的压力敏感性(0.111 kPa-1)。
电阻响应信号在60%机械负载的100个循环后保持稳定,并具有高循环重复性和稳定性。此外,研究人员还演示了PFSS在原位人体运动检测(包括步态分析和手指运动)中的实际应用,证明了它是制备智能可穿戴设备的有前途的材料。
这项研究表明,牺牲成型工艺对于用户特定的可拉伸可穿戴设备具有巨大的潜力。
总结:
利用无限制的几何设计优势,使用具有高导电性聚合物复合材料的3D打印牺牲铸模来制备具有设计结构的传感器。然而,在温和的条件下处理模具并保持精细结构仍然是一个挑战。本文中,合成了一种双功能单体可水解的受阻脲丙烯酸酯,以形成一种交联的聚合物网络,从而防止了印刷部件在未固化树脂中的溶解。3D打印的支架可以在热水中水解,这为牺牲模具提供了有吸引力的选择。另外,通过将聚氨酯/碳纳米管复合材料浇铸到牺牲模具中来制造多孔柔性应变传感器(PFSS),这显示出高拉伸性(≈510%)和出色的可恢复性。同时,压力敏感度(0。-1)和PFSS的长期电阻。电阻响应信号在60%的大应变下经过100次压缩加载循环后几乎保持不变。得益于3D打印的设计自由度,展示了具有复杂且自定义结构的PFSS在人体运动监测中的实际应用。这些结果证明,牺牲成型工艺对于用户特定的可拉伸可穿戴设备具有巨大的潜力。