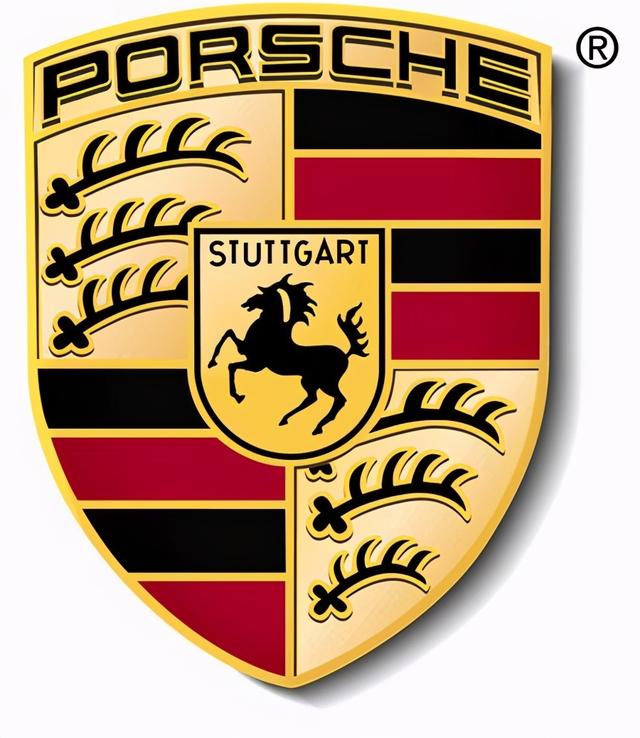
不仅造车新势力懂创新,老玩家也开始发挥想象了,保时捷正在使用3D打印技术制造更轻、更坚固、更易于使用的电动汽车传动系统部件。并且从制造到车辆驾驶都降低了排放,实现低碳环保。
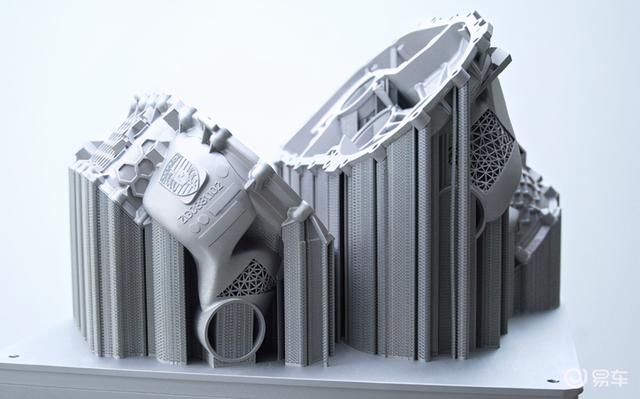
不过,保时捷并未使用消费类3D打印机。该公司有更好的制造工具,可以使用金属作为原材料,最终的结果是一个驱动单元比普通铸件轻了10%。他们可以用3D打印技术制作一些特殊的形状,使铸件的强度增加一倍,这意味着它更坚固、更轻。
东华大学柔性可穿戴电子器件直接3D打印重塑循环利用
可穿戴电子器件在生命体征监控、人机交互等领域展现了广阔的应用前景,发展迅猛,同时对材料也提出了越来越高的要求,可拉伸、弹性的导电材料成为其中磅礴兴起的热点方向。电子设备的使用寿命有限,它们在使用过程中不可避免地会发生损坏并丧失功能,成为电子
3D打印也给保时捷带来了其他好处。首先,蜂窝结构(显然不像铸造那样容易)减少了外壳在使用过程中的振动和弯曲。这提高了整个驱动装置的声学性能。它还使单元更紧凑,更容易建立,减少了40个步骤,在组装过程中节省20分钟。它还允许他们在外壳中安装一个热交换器,这有助于为高性能创造更好的冷却效果。
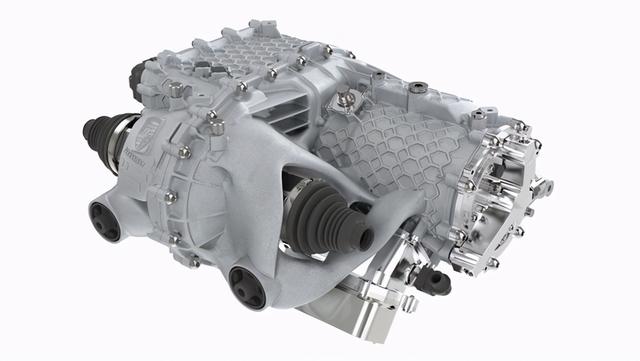
虽然该公司目前还没有计划用3D打印部件制造量产汽车,但这一过程非常适合小型生产运行和赛车应用。对于大众市场的汽车来说,在开发和测试阶段使用3D打印的能力也将使该公司受益,从而实现更快的开发和更好终端产品,最终从装配线上推出。
总而言之,这种方法给公司带来了灵活性,这对大公司来说是一件有价值的事情。